Join thousands of users earning the highest cash back and commission at over 36,000 stores and brands.
Struggling with Industrial Pumping Challenges? Here’s What Works
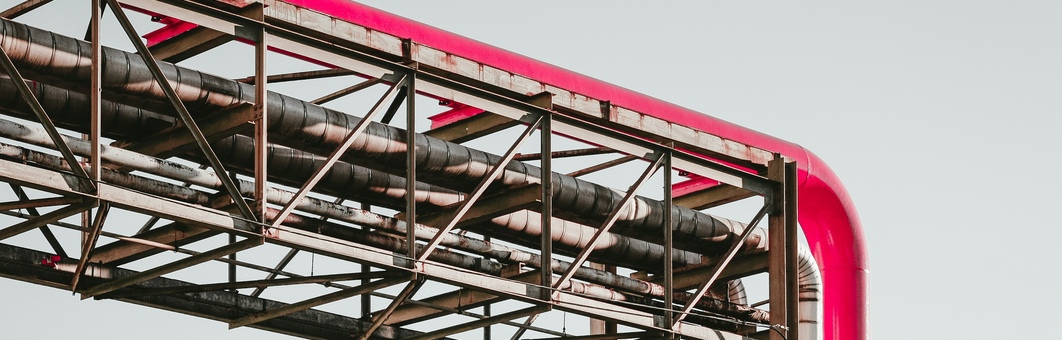
Efficient and reliable pumping solutions are essential for various industrial applications, from food processing to wastewater management. Yet, many industries face challenges such as pump failure, maintenance issues, and inefficiencies in fluid transfer. Understanding these challenges and adopting the right solutions can significantly enhance operational efficiency and reduce downtime. This article explores common industrial pumping challenges and offers practical strategies to address them effectively.
Common Issues in Industrial Pumping
Industrial pumping systems are integral to maintaining the flow of materials in manufacturing, processing, and distribution. However, they are not without challenges. Here are some common problems:
- Clogging and Blockages: Pumps dealing with viscous or solid-laden fluids often experience clogging, leading to reduced efficiency and increased maintenance.
- Leakages: Poor seals or excessive wear can result in leaks, wasting resources and potentially causing safety hazards.
- Abrasion and Corrosion: Pump components are frequently exposed to abrasive and corrosive materials, which can significantly shorten their lifespan.
- Energy Inefficiency: Outdated or improperly selected pumps often consume more energy than necessary, driving up operational costs.
To tackle these challenges, industries need tailored solutions that align with their specific requirements, ensuring longevity and reliability in their pumping systems.
Selecting the Right Pump for the Job
Choosing the right type of pump for your application is a crucial step in addressing industrial pumping challenges. Various factors, including fluid viscosity, temperature, and flow rate, influence the selection process. A mismatch between pump type and application can lead to inefficiencies, increased wear, and higher costs. For industries dealing with thick or abrasive fluids, rotary lobe pumps offer an effective solution. These pumps excel in handling viscous materials and solids while maintaining consistent flow rates. Their design minimizes shear, making them ideal for applications requiring gentle handling of sensitive products, such as in the food and beverage industry.
Maintenance Strategies to Prolong Pump Life
Even the most advanced pumps require regular maintenance to perform at their best. Neglecting maintenance can lead to breakdowns, unplanned downtime, and costly repairs. Here are some strategies to extend the life of your industrial pumping systems:
- Routine Inspections: Regularly check for signs of wear, such as unusual noises, vibrations, or temperature changes. Early detection of issues can prevent more significant problems.
- Seal and Bearing Replacement: Seals and bearings are often the first components to wear out. Replacing them proactively ensures the pump operates efficiently.
- Cleaning and Flushing: Pumps used in applications prone to clogging should be cleaned and flushed periodically to prevent blockages.
- Lubrication: Proper lubrication of moving parts reduces friction and wear, extending the life of the pump.
Adopting a preventive maintenance schedule not only minimizes unexpected downtime but also helps maintain optimal performance levels over the pump’s lifespan.
Modern Innovations in Industrial Pumping
Advancements in pump technology are revolutionizing the way industries manage fluid transfer. Innovations such as smart pumps equipped with IoT (Internet of Things) sensors allow for real-time monitoring of performance metrics like pressure, temperature, and flow rate. These systems provide valuable data, enabling predictive maintenance and reducing the risk of failures.
Additionally, energy-efficient pumps are gaining popularity as industries aim to reduce their carbon footprint and operational costs. Variable frequency drives (VFDs) enable pumps to adjust their speed based on demand, optimizing energy consumption without compromising performance.
Improving Efficiency and Sustainability
Efficiency and sustainability go hand in hand when it comes to industrial pumping systems. To achieve these goals, businesses should:
- Optimize System Design: Properly designed pumping systems minimize energy losses and improve overall performance. This includes selecting the correct pipe size, minimizing bends, and ensuring adequate pump placement.
- Invest in High-Quality Materials: Pumps made from corrosion-resistant materials, such as stainless steel or composite alloys, offer superior durability in harsh conditions.
- Train Operators: Ensuring that staff understands how to operate and maintain pumping systems correctly can significantly impact efficiency and longevity.
By implementing these measures, industries can enhance their pumping systems’ performance while aligning with sustainability objectives.
6. Choosing Trusted Suppliers
Working with reliable suppliers is a critical factor in overcoming industrial pumping challenges. A dependable supplier not only provides high-quality equipment but also offers essential support services, such as technical guidance and maintenance. This ensures the longevity and efficiency of your pumping systems.
When sourcing different solutions, partnering with experts who understand your industry needs is invaluable. These pumps are renowned for their versatility and durability, making them an excellent choice for various applications. A trusted supplier can help you select the right model, tailor configurations to your requirements, and offer post-purchase support to address any operational concerns.
Industrial pumping challenges are inevitable, but they are not insurmountable. By understanding common issues, selecting the right pump for the job, and adopting proactive maintenance practices, businesses can overcome these hurdles and achieve seamless operations.
Lobe pumps stand out as a versatile and dependable solution for handling viscous or abrasive materials, making them a valuable asset across various industries. Incorporating modern innovations and prioritizing efficiency can further enhance performance, ensuring that your pumping systems remain a cornerstone of your industrial processes. With the right approach, industries can transform pumping challenges into opportunities for growth and sustainability, paving the way for long-term success.